Top Liquid Packaging Machine Supplier: Elevate Your Production Efficiency
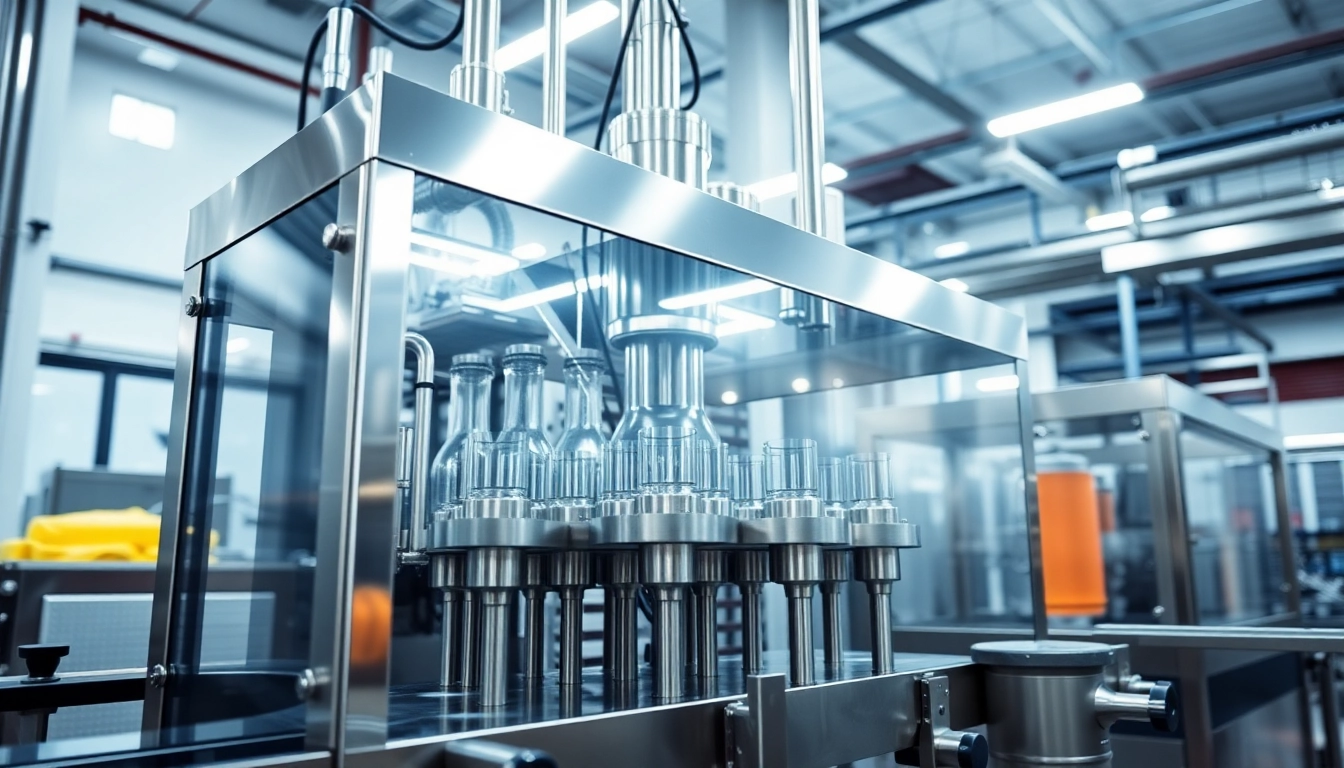
Understanding Liquid Packaging Machines
What are Liquid Packaging Machines?
Liquid packaging machines are specialized devices designed to automate the packaging of liquid products. They play a crucial role in various industries including food, pharmaceuticals, chemicals, and beverages. The primary function of these machines is to efficiently fill, seal, and package liquids into containers, ensuring that products are preserved while reducing waste and labor costs. For businesses seeking to enhance their production capabilities, collaborating with a reliable Liquid Packaging Machine Supplier is essential.
Types of Liquid Packaging Machines
Liquid packaging machines come in different types, each tailored to specific needs and product types. Understanding the available options is key for businesses to choose the right machine for their production environment:
- Filling Machines: These machines fill containers with specified volumes of liquid. Variants include piston fillers, pump fillers, and gravity fillers, each suitable for different viscosity and packaging requirements.
- Capping Machines: Post-fill, capping machines secure lids or caps on containers, ensuring product integrity and safety during transportation and storage.
- Labeling Machines: After packaging, these machines apply labels to containers for branding and identification purposes.
- Sealing Machines: Essential for maintaining product freshness, sealing machines create airtight closures on containers, preventing contamination.
- Complete Packaging Lines: These integrate multiple functions under one automated system, including filling, capping, labeling, and sometimes boxing.
Applications Across Industries
Liquid packaging machines serve a broad range of industries, each having unique requirements and standards:
- Food and Beverages: From juices to sauces, liquid packaging machines ensure that food products are packaged in sterilized, efficient environments to meet safety regulations.
- Pharmaceuticals: The precision and hygiene standards required for packaging medicines necessitate specialized machines that can handle sterile liquids without contamination.
- Cosmetics: Packaging for creams, lotions, and other liquid cosmetics must maintain product integrity and safety, often requiring unique packaging solutions.
- Chemicals: Industrial applications demand robust machinery capable of handling corrosive or volatile liquids while ensuring safety protocols are in place.
Advantages of Choosing the Right Supplier
Quality Assurance Standards
Partnering with a reputable liquid packaging machine supplier means adhering to directly established quality assurance standards. Top suppliers follow rigorous testing and validation processes to ensure their machines meet or exceed industry benchmarks, resulting in:
- Longevity and reliability of equipment
- Reduced downtime and maintenance costs
- Enhanced safety for operators
Cost-Effectiveness in Production
Cost considerations play a pivotal role in the decision-making process for manufacturers. The right supplier can provide solutions that minimize production costs by:
- Offering competitive pricing on machinery
- Providing robust after-sales service to reduce unexpected expenditures
- Suggesting pre-owned or refurbished options where applicable
Customizable Solutions for Unique Needs
Businesses often require customized machinery to meet specific packaging parameters, such as container size or product type. A forward-thinking supplier will offer:
- Custom engineering to modify existing designs
- Consultations to evaluate detailed packaging requirements
- On-site assessments to determine the best equipment layout and configuration
Key Features to Look for in a Supplier
Innovation and Technology in Machinery
Suppliers who invest in advanced technology and innovative machinery can deliver better performance and efficiency. Given the rapid evolution of packaging technology, look for suppliers who offer:
- State-of-the-art automation for increased speed and accuracy
- Integration with Internet of Things (IoT) devices for real-time monitoring and analytics
- Energy-efficient systems that reduce overall operational costs
Support and Maintenance Services
The initial purchase is only the beginning. Optimal performance of liquid packaging machines relies heavily on ongoing maintenance and support. A good supplier should provide:
- Comprehensive training programs for operators
- Timely technical support and responsive customer service
- Preemptive maintenance contracts to prevent equipment failure
Warranty and Guarantee Policies
A robust warranty indicates a manufacturer’s confidence in their product. Prospective clients should assess warranty terms, ensuring coverage includes:
- Defects in material and workmanship
- Clear procedures for claims and service
- Extended warranty options for crucial components
Leading Liquid Packaging Machine Suppliers
Comparison with Industry Leaders
Understanding how various suppliers stack up against industry standards is essential for making an informed decision. Here’s a look at some notable suppliers:
- Accutek Packaging Equipment Company: Renowned for a wide variety of filling machines suitable for various liquid types, their equipment is designed to be user-friendly and reliable.
- IPharmachine: Known for the DXD-80Y Automatic Liquid Packaging Machine, this supplier specializes in food, drink, and pharmaceutical applications, offering machinery that meets stringent industry standards.
- Viking Masek: Their focus on bagging high-viscosity liquids makes them a preferred choice for companies handling thick creams and gels.
Success Stories of Noteworthy Clients
Success stories highlight the practical impact of quality machinery, showcasing how leading suppliers have helped clients enhance their production capabilities:
- A leading food manufacturer collaborated with Accutek to reduce its filling time by 30%, significantly boosting productivity.
- IPharmachine’s innovative packaging solutions enabled a pharmaceutical company to improve its product shelf-life by integrating advanced sealing technology.
- Viking Masek supplied customized solutions that allowed a cosmetics brand to expand its product line, accommodating various viscosities without sacrificing production speed.
Market Trends and Future Directions
Industry experts predict that the liquid packaging landscape will evolve significantly in response to consumer demands and regulatory pressures, including:
- Increased automation with robotics and AI, aiming to streamline packaging processes further
- Developments in sustainable packaging materials, driven by environmental concerns and consumer preferences
- The adoption of digital printing technologies for customized packaging solutions
Getting Started with a Liquid Packaging Machine Supplier
Steps to Identify Your Packaging Needs
To partner successfully with a liquid packaging machine supplier, businesses need to identify their unique packaging needs by following these steps:
- Assess the type of liquid products being packaged, including viscosity and volume requirements.
- Determine the desired packaging format (bottles, pouches, boxes) and sizes.
- Evaluate production volume needs to decide on the type of automation required.
Requesting Quotes and Proposals
The next step entails reaching out to potential suppliers for quotes. Here are some best practices:
- Prepare a detailed request, specifying all technical requirements and desired features.
- Ask for timeframes on delivery and installation and clarify warranty and support terms.
- Compare quotes not only on price but also on the value of service and technology being offered.
Understanding Installation and Training Processes
Having the right installation and training programs in place is crucial for the successful implementation of new machinery. Key considerations include:
- Confirming that the supplier provides on-site installation and calibration services.
- Ensuring comprehensive training for operators and maintenance teams to maximize machine utilization.
- Establishing ongoing training sessions to accommodate updates or new personnel.
Leave a Reply