Maximize Efficiency with Advanced Thermal Management Materials for Electronics
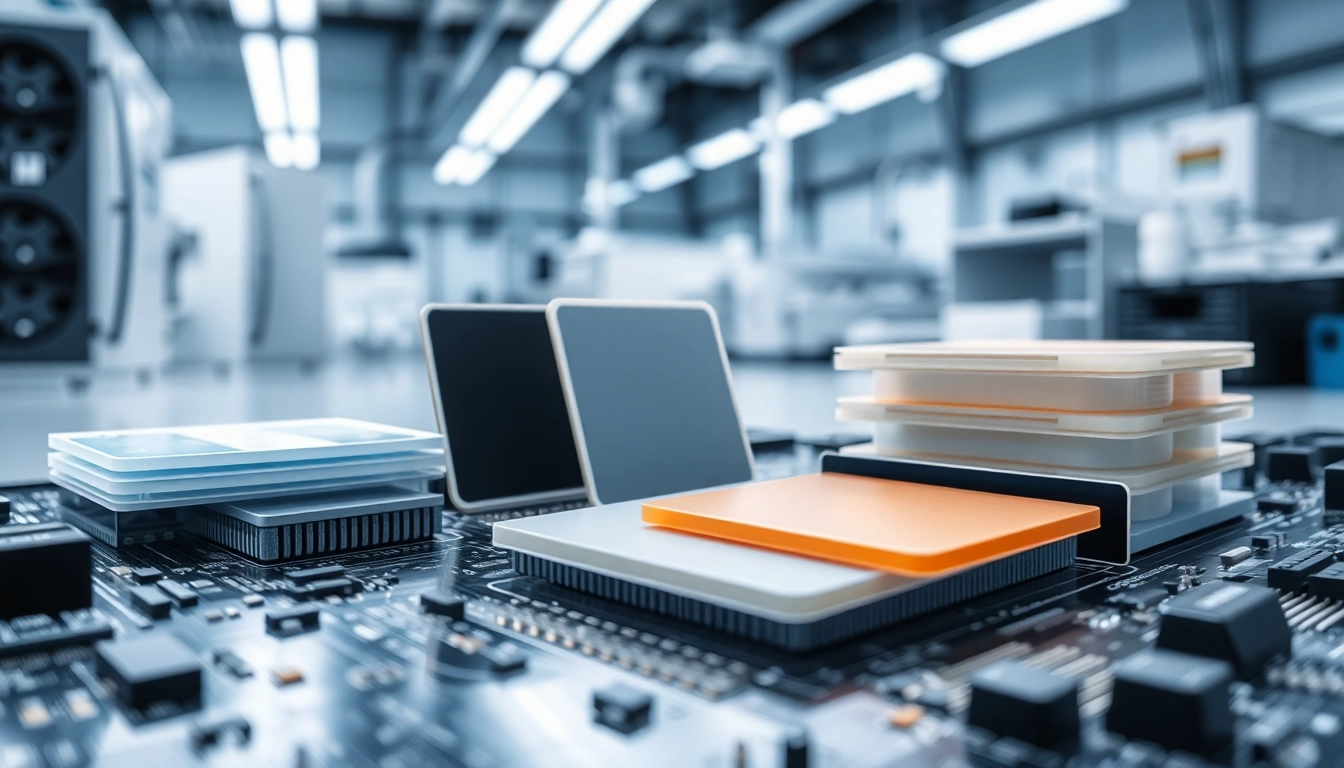
Understanding Thermal Management Materials
Definition and Importance
In today’s high-performance electronics, thermal management is a critical aspect that cannot be overlooked. Thermal management materials refer to a specialized range of products designed to efficiently dissipate heat, ensuring the reliable operation of electronic components. Excess heat can lead to performance degradation, reduced lifespan, or even catastrophic failure. Thus, selecting the right thermal management materials is vital in protecting sensitive electronic structures while improving their overall performance and efficiency.
Types of Thermal Management Materials
Thermal management materials encompass a variety of types, each tailored for specific applications and thermal management needs:
- Thermal Interface Materials (TIMs): These include thermal pads, pastes, and adhesives that provide a bridge for heat transfer between components.
- Gap Fillers: These materials are used to fill the spaces between heat-generating components and heat sinks, improving thermal contact.
- Thermal Tapes: Adhesive tapes designed for thermal conductivity provide support and adhere various components in electronic designs.
- Phase Change Materials (PCMs): These materials absorb, store, and release thermal energy during phase changes, offering dynamic heat management.
- Thermal Gels: Gel-like materials that maintain a soft and conformable structure for efficient heat transfer in varied applications.
Applications in Electronics
Thermal management materials are employed across various sectors in electronics, including:
- Consumer Electronics: Used in smartphones, laptops, and tablets to maintain optimal operating temperatures and enhance performance.
- Computing: Essential in server systems and data centers where excessive heat generation is prevalent.
- Automotive: Critical for battery thermal management, particularly in electric vehicles which utilize thermal management systems to ensure battery efficiency and safety.
- Telecommunications: Required in network infrastructure to mitigate heat in routers, switches, and transmission equipment.
Key Features of Thermal Management Materials
Thermal Conductivity and Performance
The primary feature of thermal management materials is their thermal conductivity, which is quantified by the material’s ability to conduct heat. High-performing materials, such as those manufactured by leading companies like DuPont and Henkel, offer conductivity ratings measured in Watts per meter Kelvin (W/mK), with some materials designed for specific applications achieving values exceeding 25 W/mK.
Material Composition and Structure
The efficacy of thermal management materials is affected by their composition. Various polymers, ceramics, metals, and composites are used, allowing for tailored approaches based on thermal, mechanical, and electrical requirements. For example:
- Materials like silicones provide flexibility and durability.
- Ceramic-based materials offer high thermal stability.
- Graphite-based materials are lightweight yet provide excellent thermal conduction.
Durability and Longevity
Durability is crucial as thermal materials often operate under varying temperatures and environmental conditions. High-quality thermal management materials must withstand thermal cycling without degradation, maintaining their properties over extended periods. This longevity reduces the need for frequent replacements, thus improving overall efficiency and cost-effectiveness in electronic systems.
Selection Criteria for Optimal Thermal Management Materials
Evaluating Thermal Resistance
When choosing thermal management materials, thermal resistance is a critical metric. It dictates how well a material can resist heat flow, affecting its cooling performance. Factors such as thickness, surface finish, and the specific application context should be used to evaluate thermal resistance effectively.
Compatibility with Electronic Components
Each electronic component has unique material compatibility needs. Selecting thermal management materials that can bond well with surfaces, endure mechanical stress, and possess compatible thermal expansion coefficients is essential. A mismatch can lead to ineffective thermal transfer and component failure.
Cost vs. Performance Analysis
While it’s tempting to select the least expensive option, it’s essential to balance cost with performance. High-quality thermal management materials often lead to lower long-term costs due to increased reliability and efficiency. Developing a cost-performance analysis to compare options can prevent future expenditures related to equipment failure.
Installation Practices and Best Procedures
Surface Preparation and Application Techniques
Proper installation of thermal management materials can significantly impact their effectiveness. Surface preparation is crucial; surfaces should be clean, ideally free from dust and grease, and conditioned to improve adhesion. Various application techniques include:
- Using spreaders for thermal paste to achieve even layers.
- Proper alignment of thermal pads on heat-generating components.
- Adhering thermal tapes with sufficient pressure for optimal contact.
Common Mistakes to Avoid
Several common pitfalls can greatly diminish thermal management performance:
- Using too little material, which can lead to air gaps and increased thermal resistance.
- Over-applying materials, resulting in wasted resources and potential contamination.
- Inadequate curing or drying time, impacting adhesion and performance.
Maintenance and Monitoring Best Practices
Routine maintenance and monitoring of thermal management systems are vital for longevity and efficiency. Recommended practices include:
- Regular inspections of thermal interfaces for wear or degradation.
- Measuring thermal performance with infrared thermography to detect hotspots.
- Replacing materials showing signs of wear or reduced performance proactively.
Future Trends in Thermal Management Materials
Innovations in Material Science
The future of thermal management materials is ripe with innovations. Advanced materials, such as nanocomposites and metal matrix composites, are being developed to enhance thermal conductivity while minimizing weight. Novel formulations will also likely improve performance metrics and offer better thermal stability.
Eco-friendly Materials and Sustainability
As the push for sustainability grows, thermal management materials are evolving toward eco-friendly compositions. Biodegradable materials and those using renewable resources are on the rise, offering manufacturers greener options to reduce their environmental footprints.
Market Outlook and Predictions
Forecasts indicate significant growth in the thermal management materials market, driven by rising demand in consumer electronics, electric vehicles, and renewable energy applications. Companies investing in R&D and promoting innovative solutions will secure a competitive advantage in this rapidly evolving industry.
Leave a Reply