Leading Practices in Piping Stress Analysis for Effective Engineering Solutions
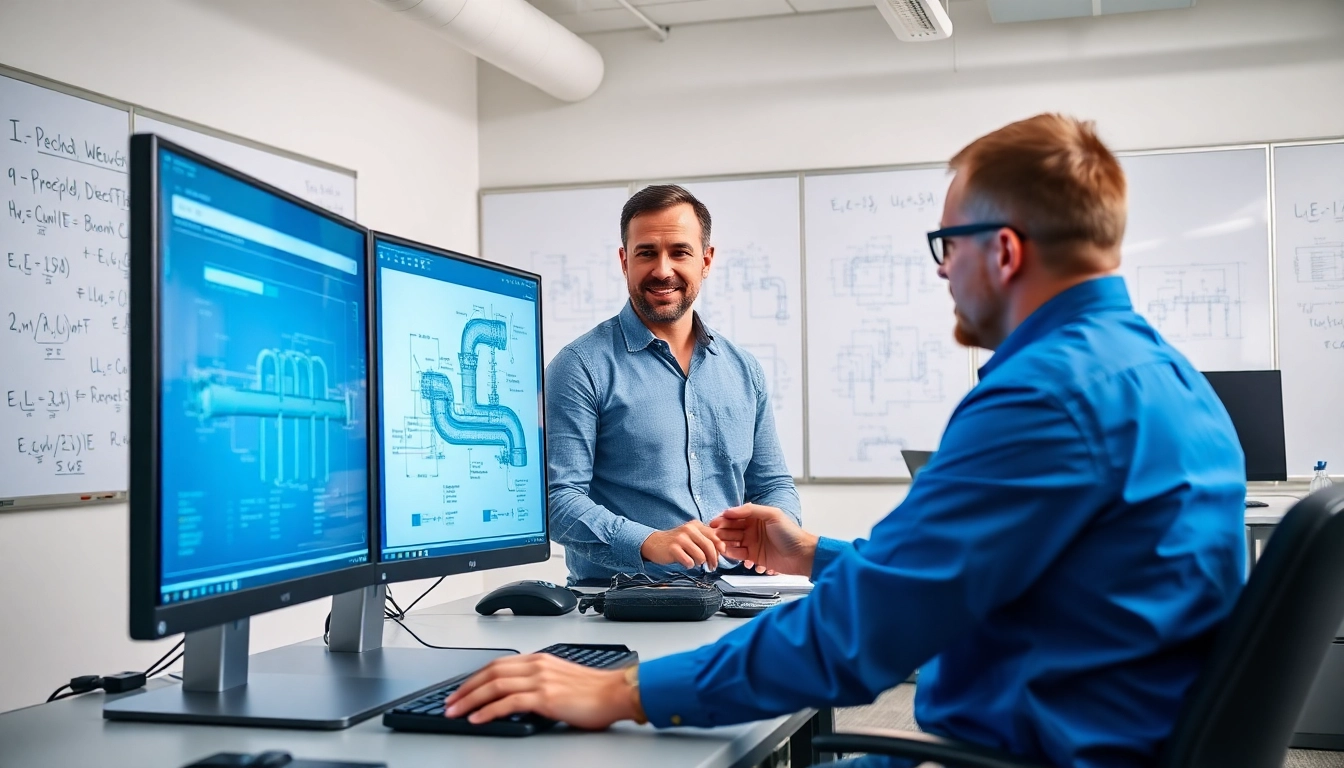
Understanding Piping Stress: Key Concepts
Piping systems are crucial in various engineering domains, primarily for transporting fluids and gases in industries like oil and gas, power generation, and chemical processing. Within these systems, piping stress analysis plays a vital role in ensuring structural integrity and operational efficiency. This article will delve deep into what piping stress analysis entails, its significance, and the methodologies used to evaluate piping systems effectively. For thorough assistance in this area, employing a reliable piping stress Analysis Company can be immensely beneficial.
What is Piping Stress Analysis?
Piping stress analysis is a branch of engineering that focuses on evaluating the stresses, strains, and overall behavior of pipe systems under various conditions. The analysis considers factors like temperature variations, internal and external pressures, and mechanical loadings which could cause deformation in piping structures. Engineers utilize various tools and methodologies to assess the stresses present in the piping layouts to prevent failures and ensure that these systems can handle operational demands.
Importance of Piping Stress in Engineering
Understanding and managing piping stress is crucial for several reasons:
- Safety: Stress analysis helps identify potential failure points and reduces the risk of catastrophes caused by leaks or ruptures.
- Regulatory Compliance: Many industries are governed by strict regulations, and proper stress analysis ensures compliance.
- Cost Efficiency: Accurately assessing stress can mitigate unnecessary repairs and replacements, leading to significant savings over time.
- System Longevity: Regular analysis helps prolong the lifespan of piping systems, ensuring consistent performance throughout their operational life.
Common Terminology Used in Piping Stress Analysis
Familiarity with piping stress analysis terminology is essential for effective communication and understanding of the subject. Some commonly used terms include:
- Load Cases: Various conditions under which the piping system operates, such as thermal expansion or seismic activity.
- Allowable Stress: The maximum stress that a piping system can withstand under specific conditions without failure.
- Stress Intensity: The measure of stress concentration within the material, critical for assessing failure risks.
- Footing and Supports: Structural elements that stabilize piping systems and help distribute loads evenly.
Methodologies for Piping Stress Analysis
The methodologies employed in piping stress analysis have evolved extensively over the years, transitioning from conventional manual approaches to advanced computational techniques. Let’s explore both traditional and modern methodologies.
Traditional vs. Modern Approaches
Traditional approaches to piping stress analysis often involved manual calculations and simplified models. Basic hand calculations used equations from engineering standards to predict stress points. However, these methods can be labor-intensive and may not account for complex variables accurately.
Modern piping stress analysis, on the other hand, utilizes advanced computational methods such as Finite Element Analysis (FEA), which allows engineers to simulate numerous load conditions and predict stresses with higher accuracy. These software solutions save time and resources while also providing a more thorough understanding of piping behavior under various scenarios.
Software Tools for Piping Stress Analysis
Several software tools have become prominent in the domain of piping stress analysis, providing engineers with sophisticated capabilities to perform in-depth evaluations. Some of the notable tools include:
- CAESAR II: A widely used software for analyzing piping systems and determining critical stress points.
- AutoPIPE: Provides powerful modeling features and can analyze complex piping layouts.
- ANSYS: A more general-purpose FEA tool that is highly flexible and can be adapted for piping stress analysis.
- SolidWorks: Known for its design capabilities, it also offers simulation features for stress analysis.
Best Practices in Methodology Selection
When selecting a methodology for piping stress analysis, consider these best practices:
- Project Requirements: Analyze the specific requirements of the project, taking into account the materials and operating conditions.
- Team Expertise: Choose methodologies and tools that align with your engineering team’s expertise and experience.
- Cost and Time Constraints: Balance the need for thorough analysis with available resources and project timelines.
- Integrative Approaches: Leverage both traditional calculations and modern software to ensure comprehensive assessments.
Common Challenges in Piping Stress Management
While piping stress analysis is invaluable, it also brings its own set of challenges. Addressing these challenges head-on can prevent potential issues that may arise during project execution.
Identifying Stress Points
One of the significant challenges in piping stress analysis is accurately identifying stress points that may lead to failure. Often, the locations of these stress points aren’t intuitively obvious and may require intricate modeling to discover hidden issues within a complex piping network.
To tackle this challenge, engineers should conduct thorough load case analyses and utilize high-fidelity simulation tools that can highlight areas of disproportionate stress distribution. This proactive approach can significantly enhance system safety from the outset.
Cracking and Fatigue in Piping Systems
Cracking and fatigue failures are among the most common issues in piping systems. Over time, repeated stress cycles can result in material fatigue, leading to significant challenges. Engineers must not only identify pre-existing cracks but also understand how various operational conditions contribute to fatigue.
Effective strategies involve continuous monitoring and inspection technologies, such as Non-Destructive Testing (NDT) methods, to spot fatigue before catastrophic failure occurs. Additionally, designing with advanced materials that exhibit higher fatigue resistance can mitigate this risk.
Mitigation Techniques for Stress-Related Issues
Mitigation strategies for managing stress-related issues center around a combination of approaches, including:
- Support Design: Properly designed supports can help in distributing loads evenly across piping systems, minimizing localized stress.
- Expansion Joints: Utilizing expansion joints can accommodate thermal expansion and contraction, reducing resultant stress.
- Material Selection: Choosing materials based on their stress endurance can increase system longevity and safety.
- Regular Maintenance: Regular inspections and maintenance can catch stress-related issues before they escalate into serious problems.
Real-World Applications of Piping Stress Analysis
Piping stress analysis finds application across various sectors, showcasing its versatility and necessity. Through case studies and industry examples, we can illustrate its impact truly.
Case Studies in Heavy Industry
In the heavy industry sector, one pivotal case study involved a major oil refining plant, where a substantial increase in throughput resulted in complex stress scenarios. The engineering team employed advanced piping stress analysis to evaluate the existing systems.
Through meticulous simulation and analysis, they identified critical stress points that would readily fail under the new operational conditions. Addressing these issues up front resulted in significant cost savings, improved safety, and ensured compliance with industry regulations.
Impact on Project Time and Cost Efficiency
Employing effective piping stress analysis not only safeguards systems but also has a direct impact on project time and cost efficiency. For instance, a chemical processing plant previously faced significant delays due to unanticipated failures, leading to costly downtime.
By integrating a robust stress analysis in their project workflow, they were able to preemptively identify stress points leading to a streamlined process, reduced downtime, and a substantial decrease in overall costs associated with repairs and replacements.
Compliance with Industry Regulations
Compliance with industry standards and regulations is non-negotiable in industries such as petrochemicals and utilities. Piping systems must meet specific standards to ensure safety and environmental protection.
Piping stress analysis ensures that projects abide by guidelines set forth by organizations such as the American Society of Mechanical Engineers (ASME) and the American National Standards Institute (ANSI). Regularly incorporating stress analysis helps maintain compliance and enables companies to uphold their reputations as safe operators.
Future Trends in Piping Stress Analysis
As technology advances, the field of piping stress analysis continues to evolve, adapting to new challenges and opportunities. Understanding these trends is essential for professionals aiming to stay ahead in the industry.
Advancements in Technology and Methods
The use of cutting-edge technology is at the forefront of advancing piping stress analysis methodologies. With the development of enhanced simulation software and improved computational power, engineers can now analyze more complicated models in significantly less time. Moreover, the integration of data analytics allows for more straightforward interpretation and better decision-making processes.
The Role of AI and Automation
Artificial Intelligence (AI) and automation are increasingly seen as indispensable tools in piping stress analysis. AI algorithms can analyze historical data and predict potential failure points, supporting proactive maintenance and reducing downtime, and machine learning models are poised to refine analysis procedures further.
Automated systems are also streamlining the data collection process, allowing real-time inspection and analysis of piping systems, leading to enhanced operational capabilities and safety metrics.
Preparing for the Future: Skills and Tools Needed
To stay relevant in an ever-evolving technological landscape, professionals in the field must cultivate a robust skill set complemented by appropriate tools. Key areas of focus should include:
- Technical Proficiency: A strong grasp of modern engineering principles, software, and simulation methodologies is crucial.
- Data Analysis Skills: As technologies become more data-driven, understanding how to interpret and utilize data for decision-making will be paramount.
- Continual Learning: Commitment to ongoing education through certifications, workshops, and conferences is essential for keeping up with industry advancements.
- Collaboration Skills: Multi-disciplinary collaboration is vital for effective piping stress analysis as teams often consist of diverse engineering backgrounds.
Leave a Reply