Essential Insights on Cutting Equipment: Types, Uses, and Best Practices
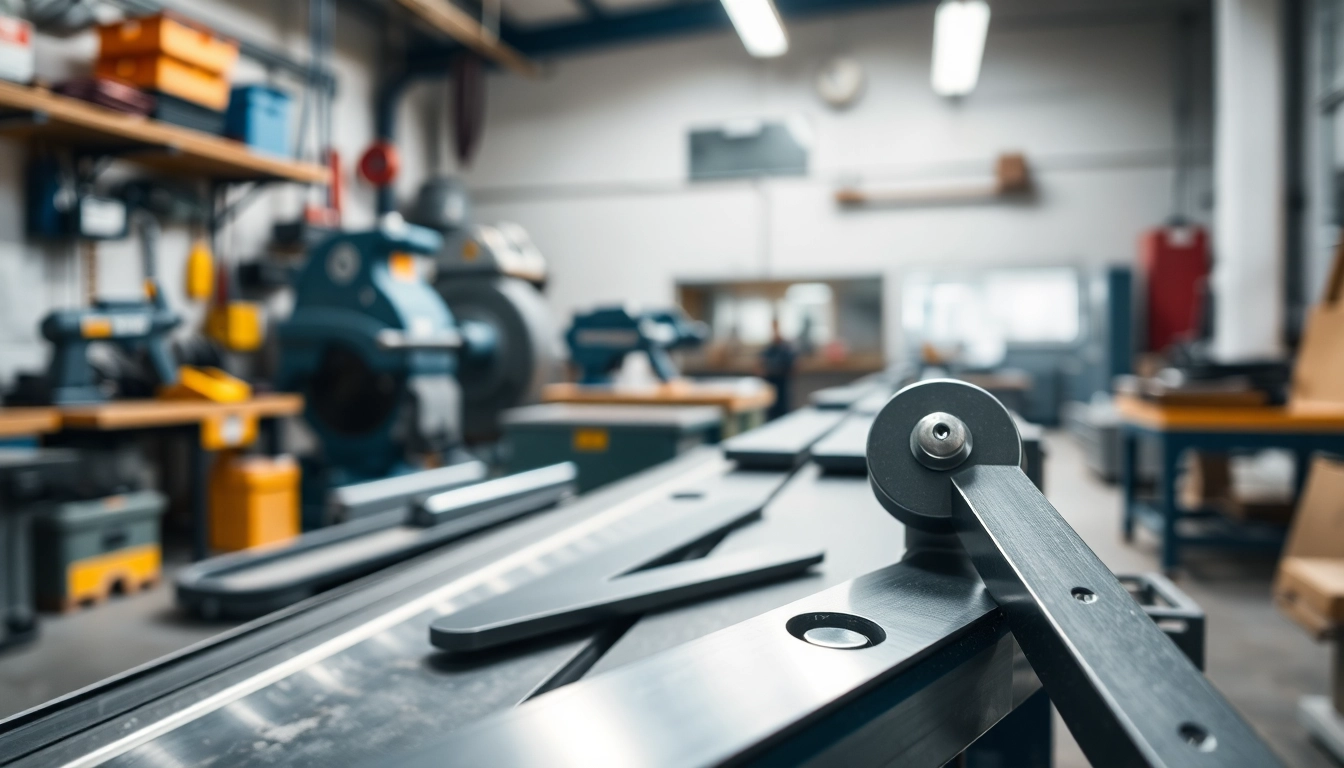
Understanding Cutting Equipment
In the realm of manufacturing and various industrial sectors, the significance of cutting equipment cannot be overstated. These tools are essential for shaping, slicing, and crafting materials into desired forms and sizes. As industries evolve, the necessity to adapt to changing demands and technologies grows, making the selection of appropriate cutting equipment all the more critical.
The Importance of Choosing the Right Cutting Equipment
Choosing the right cutting equipment is a pivotal decision in ensuring operational efficiency and product quality. The effectiveness of production processes often hinges on equipment choices that align with specific project requirements. The right tools not only enhance productivity but also minimize operational costs by reducing waste and prolonging the service life of machinery.
Failure to select suitable cutting tools can lead to a cascade of issues, including poor-quality outputs, increased downtime, and higher maintenance costs. Each project may require different types of equipment based on material properties, production volume, and end-use applications, making proper selection crucial.
Types of Cutting Equipment Available
Cutting equipment encompasses a diverse array of tools designed for various applications. The primary categories include:
- Laser Cutters: Ideal for precision work, laser cutters use focused light beams to cut materials with accuracy and minimal waste.
- Plasma Cutters: Utilizing high-velocity ionized gas, plasma cutters are excellent for cutting thick metals and provide speed and efficiency.
- Waterjet Cutters: These machines rely on high-pressure water mixed with abrasive materials to cut a variety of hard materials without generating heat.
- Band Saws: Commonly used in woodworking and metalworking, these saws are versatile and capable of cutting intricate shapes.
- Oxy-Fuel Cutters: Utilizing a flame for cutting metal, these cutters are robust and widely used in industrial applications.
- Shears and Snips: Manual or powered tools designed for straightforward cuts in sheet metal and thin materials.
Key Features to Consider When Selecting Tools
When selecting cutting equipment, several key features should be evaluated:
- Cutting Speed: The speed at which a machine can operate can significantly affect production rates and output.
- Material Compatibility: Understanding the types of materials the equipment can handle is critical for ensuring effective results.
- Precision and Tolerance: Different applications may require varying levels of precision; select equipment that meets these specifications.
- Ease of Use: Equipment that is intuitive and user-friendly can minimize training time and enhance workforce efficiency.
- Maintenance Requirements: Consideration of how much maintenance the equipment will need helps in calculating total cost of ownership.
- Cost: While it’s tempting to go for the cheaper option, understanding the long-term implications of equipment selection is crucial.
Applications of Cutting Equipment
Industries Utilizing Cutting Tools Effectively
Cutting equipment finds applications in a wide range of industries, each with its unique requirements:
- Aerospace: Cutting tools in the aerospace industry are utilized to manufacture complex components with extreme precision.
- Automotive: From body panels to engine components, cutting equipment is essential for producing vehicle parts efficiently.
- Construction: In the construction industry, tools are employed to cut materials such as metal, wood, and concrete to specified dimensions.
- Metals Manufacturing: The metalworking industry relies heavily on cutting tools for shaping and finishing metal products.
- Textiles: Specialized cutting equipment is used to slice fabrics with accuracy to yield the desired patterns and sizes.
Common Challenges and Solutions in Equipment Usage
While cutting equipment is vital for efficiency, challenges often arise:
- Blade Wear: Frequent and intense cutting operations can lead to blade wear, resulting in diminished performance. Regular maintenance and timely replacement of blades can mitigate this issue.
- Material Distortion: Heat generated during cutting can cause warping in materials. Utilizing waterjet or laser cutting can reduce heat-related distortions.
- Equipment Downtime: Regular servicing and proper training for users can minimize the risks associated with unexpected downtime.
Case Studies: Successful Implementation of Cutting Equipment
Examining real-world implementations of advanced cutting equipment demonstrates the benefits of selecting the right tools:
- Case Study 1 – Automotive Sector: A leading automobile manufacturer adopted laser cutting technology to streamline its production processes, achieving a 30% reduction in production time while enhancing the precision of component cuts.
- Case Study 2 – Aerospace Industry: An aerospace parts manufacturer integrated waterjet cutting systems, significantly reducing material waste and improving cutting accuracy, leading to enhanced performance of the final products.
Best Practices for Operating Cutting Equipment
Safety Precautions When Using Cutting Tools
Safety is paramount in operating cutting equipment. Adhering to standard safety practices can prevent accidents and injuries:
- Personal Protective Equipment (PPE): Always wear appropriate PPE, including gloves, goggles, and ear protection, based on the equipment in use.
- Training: Ensure all operators are adequately trained on the specific equipment they are using.
- Follow Manufacturer Guidelines: Always operate equipment within the parameters outlined in the manufacturer’s manual.
- Workspace Organization: Maintain a clutter-free area around the cutting equipment to minimize hazards.
Maintenance Tips for Longevity of Equipment
To ensure the longevity of cutting tools, regular maintenance is essential:
- Regular Inspections: Routine checks for wear and tear enable early detection of potential issues.
- Proper Lubrication: Keeping moving parts adequately lubricated reduces friction and wear.
- Calibrating Equipment: Regularly calibrate cutting tools to maintain accuracy and performance.
Training and Skill Development for Users
Investing in training fosters a safer, more efficient work environment. Key training elements include:
- Hands-On Training: Providing practical, hands-on experience helps users become familiar with equipment operation.
- Continuous Learning: Encourage ongoing education to keep abreast of new technologies and practices in cutting equipment.
- Skill Assessments: Frequent assessments can help identify areas where additional training may be beneficial.
Staying Ahead in Cutting Equipment Technology
Innovations in Cutting Tools and Techniques
The cutting equipment landscape is constantly evolving, with innovative technologies and techniques transforming operations:
- Intelligent Cutting Systems: Integration of AI and machine learning for optimized cutting paths and reduced cycle times.
- Automation: The rise of automated cutting systems enhances production efficiency and consistency while reducing labor costs.
- Hybrid Technology: Equipment that combines multiple cutting techniques (e.g., laser and waterjet) to enhance versatility and capability.
Evaluating Performance Metrics of Cutting Equipment
Tracking performance metrics is essential for assessing equipment effectiveness:
- Cutting Speed: Measurement of speed can help inform operational efficiency.
- Material Usage: Keeping track of scrap rates can identify areas for improvement.
- Downtime: Monitoring operational downtime can lead to better maintenance schedules and reduced costs.
Future Trends in Cutting Technology
The future of cutting equipment looks promising, with trends hinting at further advancements:
- 4D Printing: Emerging technologies may allow for real-time cutting adjustments based on material response.
- Sustainable Practices: A focus on eco-friendly practices, including energy-efficient machinery and recycling of materials.
Choosing the Right Partner for Cutting Equipment
Criteria for Selecting Equipment Suppliers
When sourcing cutting equipment, evaluating suppliers is critical. Key criteria include:
- Reputation: A supplier’s track record for quality and service is an essential consideration.
- Product Range: Consider the breadth of product offerings to ensure a comprehensive solution.
- Technical Support: Evaluate the level of technical support and customer service available from suppliers.
Importance of Post-Purchase Support and Services
Post-purchase support plays a vital role in maximizing equipment performance:
- Warranty and Repair Services: Understanding warranty coverage and access to repair services can protect your investment.
- Training Opportunities: Ongoing training from suppliers can enhance user competence and safety.
Building Strong Relationships with Vendors
Developing strong, collaborative relationships with equipment vendors can yield long-term benefits:
- Open Communication: Encouraging dialogue fosters trust and facilitates timely problem resolution.
- Mutual Growth: A partnership focused on mutual growth can lead to better customized solutions and improved service.
Leave a Reply