Precision Applications of High-Performance Adhesive Films at https://www.makobond.com/adhesives-films for Aerospace and Automotive Industries
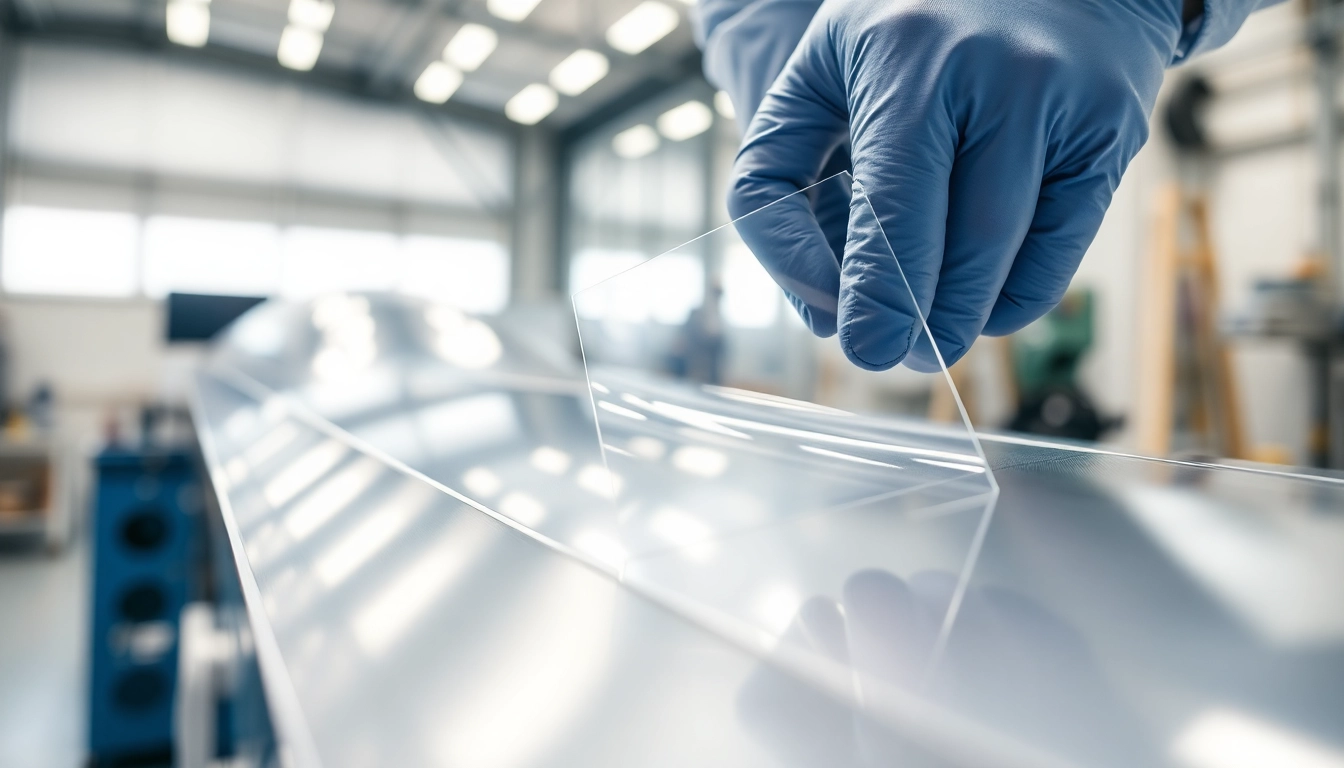
The Importance of Adhesive Films in Modern Engineering
In the ever-evolving landscape of engineering and manufacturing, adhesive films represent a cornerstone technology that facilitates advanced bonding solutions across various industries. These precision-cast films are integral to creating robust, consistent bonds in applications ranging from aerospace to automotive. They offer a clean and controlled bonding environment, which is crucial for ensuring the performance and longevity of composite materials that are increasingly used due to their lightweight yet strong properties. Understanding these adhesive solutions is essential for engineers and manufacturers looking to enhance their production processes. More detailed insights can be found at https://www.makobond.com/adhesives-films.
Understanding Adhesive Film Technologies
Adhesive films are pre-formed layers of adhesive supported on a carrier film. They are ready to bond surfaces when activated by heat or pressure, which is a crucial factor in many industrial processes. The technology behind these films involves an understanding of polymer science, where engineered formulations are designed to meet specific performance criteria, including shear strength, peel strength, and thermal stability.
Modern adhesive films may utilize various polymers such as epoxy, polyurethane, or acrylics. Each of these materials provides unique benefits, such as superior adhesion to different substrates or enhanced resistance to various environmental conditions, thus broadening the applications they can be used for. Continuous advancements in adhesive technologies promise improvements in their performance and usability.
Key Applications in Aerospace and Automotive
Aerospace and automotive industries are perhaps the most demanding sectors when it comes to adhesive bonding. In aerospace, adhesive films are used extensively for bonding composite structures, which are crucial for reducing weight and enhancing fuel efficiency. The films allow for high-performance bonding with excellent fatigue resistance, which is necessary for aircraft that endure extreme stress during flight.
In the automotive sector, lightweight materials are increasingly integrated into vehicle designs to comply with stringent fuel economy regulations. Adhesive films play a critical role not only in bonding materials like metals, plastics, and composites but also in providing sound dampening and thermal insulation properties.
Benefits of Using High-Quality Adhesive Films
Choosing high-quality adhesive films leads to several advantages, including:
- Enhanced Bond Strength: Superior adhesive formulations yield stronger bonds, which are crucial for structural integrity.
- Weight Reduction: Films are generally lighter compared to traditional bonding methods, contributing to reduced overall weight in aerospace and automotive applications.
- Improved Aesthetics: Adhesive films allow for clean bonding, reducing visual defects and improving the final appearance of products.
- Operational Efficiency: The ease of application and faster curing times lead to increased production speed and reduced manufacturing costs.
Types of Adhesive Films: Features and Specifications
Comparing Different Adhesive Film Types
There are several types of adhesive films available on the market, each designed to suit different applications. Common types include:
- Thermoplastic Adhesive Films: These include films that melt and flow when heated, allowing for easy application.
- Thermosetting Adhesive Films: Once cured, these films do not melt, resulting in a permanent bond that is ideal for high-temperature applications.
- Specialty Adhesive Films: Designed for niche applications, these films may include features such as high-resistance to chemicals, UV stability, or specific flexibility characteristics.
Performance Metrics for Aerospace Applications
Performance metrics are vital for assessing the suitability of adhesive films in aerospace applications. Key metrics include:
- Shear Strength: This metric measures the force required to shear the adhesive layer, reflecting the bond’s robustness under load.
- Peel Strength: This assesses the adhesive’s ability to withstand forces that attempt to separate it from the bonded surface.
- Thermal Stability: It determines how well the adhesive performs under extreme temperatures, a common condition in aerospace environments.
- Durability: Includes factors like fatigue resistance and longevity under various operational conditions.
Material Composition and Properties
The material composition of adhesive films is a critical factor influencing their performance. This includes:
- Base Polymer: The choice of polymer determines the fundamental properties of the adhesive film, such as flexibility, strength, and resistance to environmental challenges.
- Additives: Fillers and additives can enhance specific properties such as thermal resistance, conductivity, or UV stability, ensuring that the adhesive meets the required application standards.
- Carrier Film: The support layer provides structural integrity and can affect the ease of application and handling of the adhesive film.
Installation Techniques for Effective Bonding
Preparation and Surface Treatment Requirements
Proper bonding starts with the preparation of the surfaces that will be bonded. This includes cleaning to remove any contaminants such as oils, dust, or existing coatings that may interfere with adhesion. The use of solvents or mild abrasives is common in surface preparation.
Surface roughening can also enhance bond strength by increasing the mechanical interlocking between the adhesive and the substrate. Additionally, appropriate treatments such as plasma treatment or chemical priming may be employed to promote better adhesion, especially with challenging materials like composites or metals.
Step-by-Step Application Process
The application of adhesive films generally follows a structured process:
- Surface Preparation: Thoroughly clean and prepare surfaces for optimal bonding.
- Film Placement: Position the adhesive film onto the substrate, ensuring accurate alignment.
- Activation: Apply heat and/or pressure to activate the adhesive properties, enabling it to bond to the substrate effectively.
- Curing: Allow sufficient time for the adhesive to cure, which guarantees the bond’s integrity and strength.
Common Mistakes to Avoid During Installation
Effective installation is crucial for the success of adhesive films. Here are common mistakes to avoid:
- Inadequate Surface Preparation: Neglecting cleaning or roughening can lead to weak bonds.
- Improper Activation: Failing to meet the required temperature or pressure settings can prevent the adhesive from curing properly.
- Incorrect Alignment: Misalignment during placement can lead to uneven bonding and reduce performance.
Evaluating Adhesive Film Performance
Testing Methods for Bond Strength
To ensure the reliability of adhesive films, several testing methods are utilized to evaluate bond strength:
- Tensile Testing: Measures the force required to break the bond.
- Peel Testing: Evaluates the adhesive’s resistance to being peeled away from the substrate.
- Fatigue Testing: Simulates extended use to assess the bond’s durability over time.
Factors Influencing Adhesive Film Durability
Durability is influenced by various factors, including:
- Environmental Conditions: Temperature fluctuations, humidity, and chemical exposure can impact the performance and longevity of adhesive films.
- Mechanical Stress: Continuous loads and vibrations can lead to fatigue and eventual failure, particularly in dynamic applications.
- Quality of Application: Proper installation techniques significantly impact the final performance and durability of the adhesive bond.
Real-World Case Studies and Results
Application successes demonstrate the effectiveness of adhesive films. Case studies have shown that films used in aerospace applications result in significant weight savings while maintaining structural integrity. Similarly, in automotive applications, use of advanced adhesive films has resulted in improved production line efficiency and superior vehicle ergonomics. Compiling these results highlights the effectiveness and reliability of adhesive films as crucial components in modern engineering.
Future Trends in Adhesive Film Development
Innovative Materials on the Horizon
As research continues to progress, new materials are being developed that promise enhanced properties for adhesive films. Innovations involve bio-based adhesives that cater to sustainability requirements without compromising performance or safety. Likewise, smart adhesives that adjust their properties in response to environmental changes are on the rise, reflecting the growing trend toward intelligent materials in engineering.
Advancements in Manufacturing Techniques
Manufacturing processes for adhesive films are evolving alongside advancements in technology. Techniques such as 3D printing and advanced coating technologies allow for highly customizable adhesive solutions tailored to specific applications, promoting enhanced performance and efficiency. Additionally, this shift towards more automated manufacturing processes reduces waste and increases throughput in production lines.
The Role of Sustainability in Adhesive Film Production
Sustainability is becoming an integral factor in adhesive production, with increasing focus on minimizing environmental impact. This includes developing adhesives free from harmful solvents and reducing the carbon footprint of manufacturing processes. The push towards sustainable materials aligns with global initiatives targeting green manufacturing and responsible production.