Maximize Metal Surface Preparation: Key Insights on Needle Guns
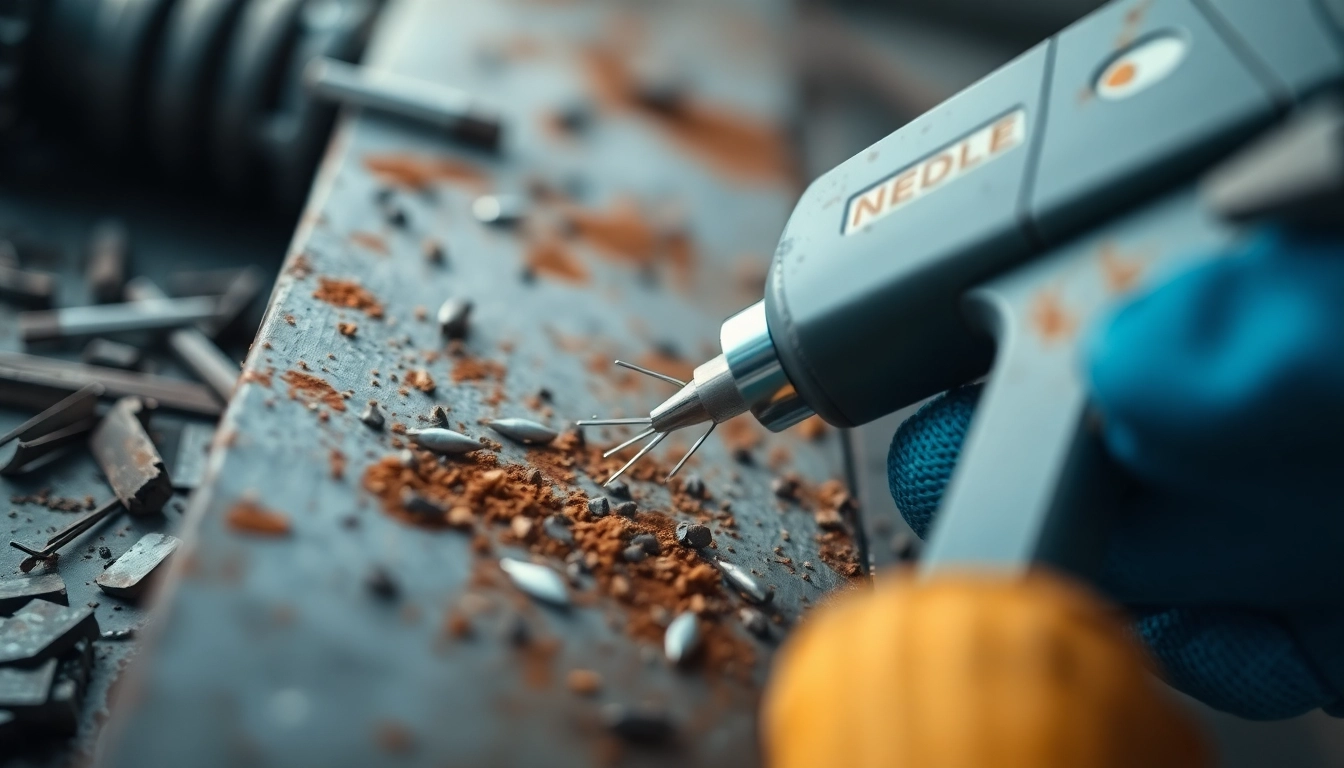
Understanding Needle Guns: Mechanism and Uses
Needle guns, also known as needle scalers, are versatile tools commonly used in metal surface preparation. They play a crucial role in removing rust, old paint, and other contaminants from metal surfaces. By employing a series of rapidly moving needles, these tools vibrate and effectively dislodge unwanted materials, making them invaluable in various industries, including automotive repair, shipbuilding, and metal fabrication. For those looking to invest in such a tool, options like the needle gun are readily available, showcasing the sophistication and utility of modern scalers.
How Needle Guns Work: The Technology Behind the Tool
At the heart of a needle gun’s design is its mechanism, which typically consists of a compressed air system that drives the tool’s needles. When activated, air is forced through the device, causing the needles to vibrate at high speeds, usually between 3,000 and 5,000 beats per minute (BPM). This rapid movement allows the needles to penetrate the surface material, effectively lifting away debris.
The needles used in these tools are often made from hardened steel, which ensures durability and effectiveness. Depending on the model, needle guns can come with different configurations of needle sizes and lengths, impacting the operational efficiency and suitability for various tasks. For example, finer needles might be used for delicate work, while stouter needles work well for heavy rust removal.
Common Applications: Where and Why to Use a Needle Gun
Needle guns are widely utilized across multiple fields due to their effectiveness in surface preparation. Here are some common applications:
- Automotive Industry: Professionals often use needle guns for cleaning vehicle parts, ensuring a proper surface for painting or welding.
- Shipbuilding and Maintenance: The marine industry relies on needle guns to remove marine growth, rust, and old paint from ships and boats.
- Construction: In construction, these tools help prepare surfaces for coatings or repairs by eliminating old paint and grime.
- Metal Fabrication: Workshops use needle guns to restore metal parts to optimal condition before further processing.
Types of Needle Guns: Pneumatic vs. Electric Models
Needle guns generally fall into two main categories: pneumatic (air-powered) and electric models. Each has distinct advantages depending on the application.
Pneumatic Needle Guns: These are typically more powerful, achieving higher BPM rates and supporting prolonged use without overheating. They require an air compressor, making them ideal for heavy-duty applications.
Electric Needle Guns: While somewhat less powerful, electric models offer greater mobility and ease of use without the need for external compressed air sources. They are perfect for light to moderate tasks, especially in indoor settings where noise and exhaust may be issues.
Choosing the Right Needle Gun for Your Project
Assessing Project Needs: Factors to Consider
Choosing the appropriate needle gun hinges on several factors:
- Project Size: Larger projects may benefit from pneumatic models for their sustained power and efficiency.
- Type of Material: Assessing the metal type and condition will guide you towards the appropriate needle size and configuration.
- Frequency of Use: If frequent use is expected, investing in a more durable model may be cost-effective in the long run.
- Budget: Prices can vary significantly, so balancing features with budget constraints is crucial.
Top Brands and Models: A Market Overview
When it comes to purchasing needle guns, several brands stand out for their reliability and performance. Some popular brands include:
- Ingersoll Rand: Known for high-quality pneumatic tools, Ingersoll Rand offers several models tailored for professional use.
- LE LEMATEC: This brand provides powerful pneumatic needle scalers renowned for their efficiency and ease of use.
- Trelawny: Their models are noted for heavy-duty use, particularly in industries where rust removal is prevalent.
- Powermate: Their electric needle scalers are ideal for light use, providing solid performance for small projects.
Reviews and User Feedback: Insights from Professionals
User feedback is invaluable when selecting a needle gun. Customers often highlight the difference in performance between pneumatic and electric models, with professionals favoring the pneumatic variants for industrial applications due to their power and speed. Conversely, DIY users often endorse electric models for home use, citing their convenience and accessibility.
Moreover, many reviews emphasize the importance of needle configuration concerning the cleaning tasks at hand. Users report that having a selection of needles can significantly enhance versatility and effectiveness.
Best Practices for Operating Needle Guns Safely
Safety Gear: Essential Equipment for Protection
When using a needle gun, safety should be a top priority. Essential safety gear includes:
- Safety Glasses: Protects eyes from flying debris.
- Hearing Protection: Reduces the impact of high noise levels, especially with pneumatic models.
- Gloves: Ensure a better grip and protect hands from sharp edges and debris.
- Respirators: If working in a confined space, a respirator can prevent inhalation of dust and contaminants.
Operating Techniques: Maximizing Efficiency and Safety
To operate a needle gun effectively, consider the following techniques:
- Maintain an Even Pressure: Apply consistent pressure while working to ensure balanced wear on the needles.
- Move Methodically: Work in sections and avoid rushing to eliminate missed spots and ensure a thorough clean.
- Keep the Tool Clean: Regularly clean the needle gun to prevent built-up debris that can hinder performance.
- Always Inspect: Check the condition of the needles before use; damaged or worn needles can compromise effectiveness and safety.
Maintenance Tips: Keeping Your Needle Gun in Top Condition
To prolong the lifespan of your needle gun, adhere to these maintenance tips:
- Clean After Each Use: Remove dust and debris to prevent clogs or jams.
- Lubricate Moving Parts: Proper lubrication minimizes wear and enhances performance.
- Regularly Check for Damage: Inspect for any signs of damage or wear; replacing parts promptly can prevent further issues.
Advanced Techniques: Achieving Optimal Results with Needle Guns
Combining Tools: Using Needle Guns with Other Equipment
For optimal results, needle guns can be used in conjunction with other tools. For instance, starting with a rotary grinder may efficiently remove heavy scale before finishing with a needle gun for a smooth surface. Additionally, using a blasting cabinet with a needle gun can achieve a polished metal finish, facilitating further coatings or treatments.
Surface Preparation Standards: What to Achieve
Every industry has its standards for surface preparation. For instance, automotive applications often require a clean metal surface for proper adhesion of paints and coatings; achieving this typically necessitates a texture-free finish. Understanding specific standards can guide the operation of a needle gun to meet or exceed these requirements.
Troubleshooting Common Issues: Effective Solutions
Even with proper use, issues can arise with needle guns. Common problems include:
- Reduced Power: Often caused by a clogged air supply line; ensure that air filters are clean and free from obstructions.
- Excessive Vibration: This can indicate worn needles; replacing them may be necessary to restore optimal function.
- Needles Breaking: Ensure the proper needle type is being used for the material; using the wrong size can lead to premature failure.
The Future of Needle Guns: Trends and Innovations
Technological Advances in Needle Gun Design
The development of needle guns has seen significant advances in technology. Modern models feature improved ergonomics, reduced noise levels, and even automated systems that enhance their usability. Additionally, some needle guns now integrate advanced pneumatic systems which regulate air flow to maximize power while minimizing operator fatigue.
Eco-Friendly Options: Sustainability in Tool Manufacturing
As industries increasingly emphasize sustainability, manufacturers are developing eco-friendly needle guns that reduce energy consumption and minimize waste. These innovations often include more efficient air consumption and materials that have lower environmental impact.
Market Predictions: What’s Next for Needle Gun Technology
The future of needle guns indicates a shift toward smarter technology, with the potential integration of IoT devices that can track usage metrics and provide real-time feedback. This data can be invaluable for operations seeking to optimize their tool performance and ensure compliance with industry standards.
Leave a Reply