Essential Guide to Walk In Freezer Repair: Tips and Best Practices for Your Business
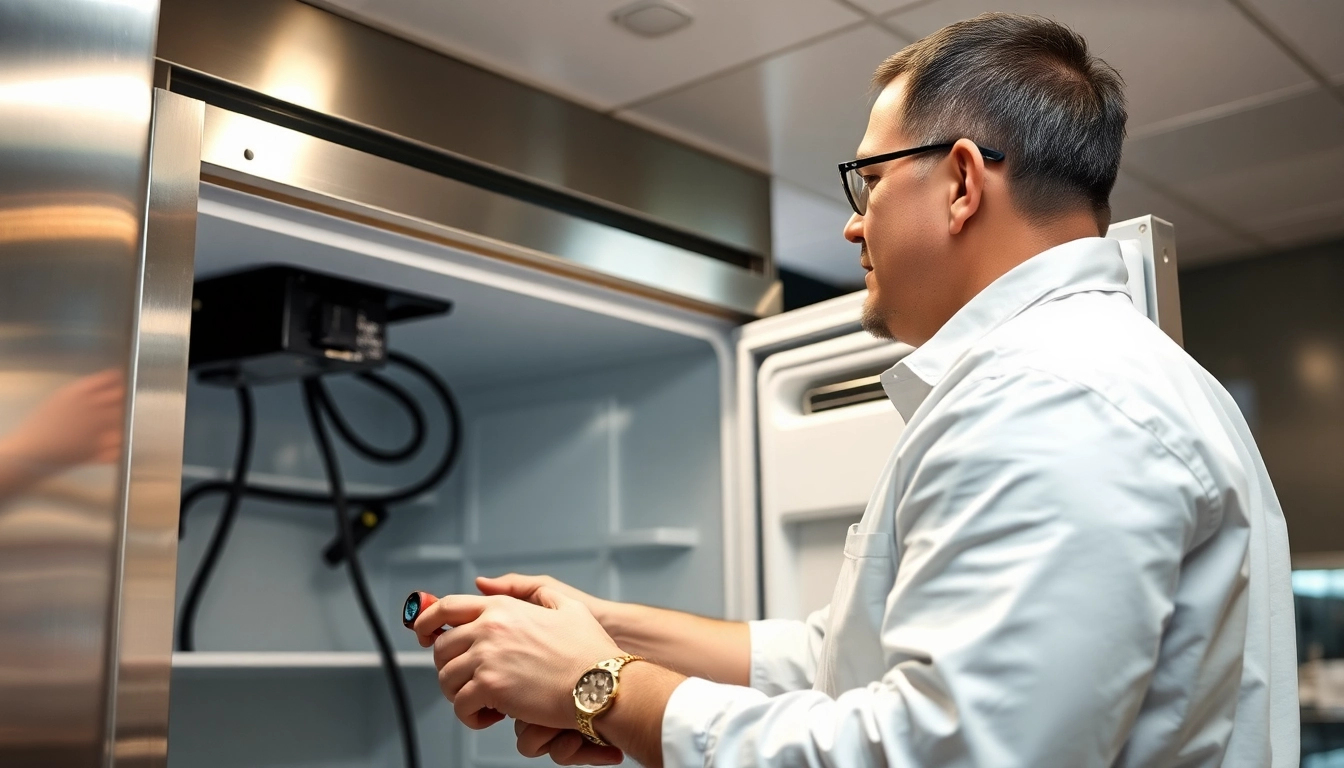
Understanding Walk In Freezer Repair Needs
Maintaining the functionality of a walk-in freezer is crucial, especially for businesses relying on precise temperature control for perishable goods. Regular checks and prompt repairs not only streamline operations but also safeguard your investment and food quality. Recognizing the necessity for walk in freezer repair can prevent minor issues from evolving into costly repairs or replacements. This guide explores common problems, maintenance practices, DIY versus professional repair decisions, emergency response strategies, and post-repair practices that can keep your freezer running efficiently.
Common Issues That Require Repair
Walk-in freezers can experience various malfunctions due to wear and tear, environmental conditions, and operational demands. Understanding common issues can significantly enhance response times. Below are several prevalent problems:
- Temperature Fluctuations: Inconsistent temperatures can jeopardize food safety. Common causes include thermostat malfunctions, clogged condenser coils, or evaporator issues.
- Door Sealing Issues: Worn or damaged door gaskets can lead to temperature loss, raising energy costs and risking spoilage.
- Compressor Failures: The compressor is the heart of your freezer’s cooling system. If it fails, the entire unit can become inoperable.
- Ice Build-Up: Excess buildup can hinder airflow, leading to inefficient cooling and increased energy consumption.
- Fan Malfunctions: Fans ensure a consistent temperature throughout the unit. Their failure can result in uneven cooling.
Signs That Indicate Your Freezer Needs Attention
Being vigilant about the operational state of your walk-in freezer can save money and prevent more serious issues. Here are key signs that indicate your freezer may need repairs:
- Unusual noises such as rattling, buzzing, or grinding sounds.
- Condensation or frost forming on the exterior or interior surfaces.
- Temperature readings that consistently exceed set levels.
- Increased energy bills without a corresponding change in usage.
- Frequent cycling on and off of the compressor.
Understanding Maintenance Versus Repair
Understanding the difference between maintenance and repair is essential for effective freezer management. Maintenance involves routine tasks meant to prevent breakdowns, while repair addresses issues that have already occurred. Regular inspections, cleaning coils, checking seals, and monitoring temperatures fall under maintenance, whereas replacing a faulty compressor or fixing a broken fan is considered repair. Establishing a proactive maintenance schedule can reduce the need for more extensive repairs down the line.
DIY vs. Professional Walk In Freezer Repair
The decision to perform repairs yourself or hire a professional depends on the complexity of the issue, your technical skills, and available resources. Evaluating the merits of both options can help you make the best choice.
When to Attempt DIY Repairs
Some repairs can be straightforward and do not require professional training. Consider attempting DIY repairs in the following scenarios:
- Replacing door gaskets if they are visibly worn or damaged, using readily available kits.
- Cleaning condenser coils to improve efficiency.
- Checking and replacing light bulbs or simple electrical components.
Before attempting DIY repairs, ensure you have the proper tools and follow safety protocols, including wearing gloves and ensuring that the freezer is unplugged when necessary.
Benefits of Hiring Professional Technicians
While some repairs can be executed as DIY tasks, the benefits of hiring a professional technician often outweigh the advantages of DIY:
- Expertise: Professionals possess specialized knowledge and experience, enabling them to diagnose and fix issues quickly and correctly.
- Warranty Protection: Hiring certified technicians can help maintain equipment warranties, as improper repairs could void them.
- Safety: Many repairs involve electrical systems and refrigerants, which can be hazardous to handle without training.
- Time Savings: Professionals usually have access to tools and parts, allowing for quicker repairs compared to the DIY approach.
Cost Analysis: DIY Repairs Versus Professional Services
Costs for repairs can vary widely based on the problem’s complexity. Factors include:
- DIY Costs: Typically limited to parts, which can range from $10 to $300, depending on the repair.
- Professional Services: The average cost for a professional to repair a walk-in freezer can range from $200 to $2,000, influenced by labor rates and parts required.
While DIY repairs may save on labor costs, investing in professional support for complex issues may ultimately result in savings by preventing further damage.
Preventative Measures for Walk In Freezer Longevity
Consistent preventative measures can significantly extend the life of your walk-in freezer. Understanding what tasks are necessary can mitigate repair needs and optimize performance.
Essential Maintenance Tasks to Perform Regularly
Incorporating routine maintenance tasks into your schedule can help keep your walk-in freezer functioning properly. Key practices include:
- Regularly cleaning condenser coils to prevent overheating.
- Checking door seals for tears and replacing them to maintain efficiency.
- Ensuring proper drainage to prevent ice buildup from condensation.
- Testing backup power sources if available to maintain functionality during outages.
- Monitoring refrigerant levels and looking for leaks to prevent compressor strain.
Tips for Optimizing Freezer Performance
Beyond standard maintenance, consider these performance-enhancing tips:
- Temperature Monitoring: Install a digital thermometer to ensure the temperature remains stable.
- Air Flow Maintenance: Ensure air vents are clear and that items stored in the freezer do not obstruct airflow.
- Regular Inventory Checks: Keep track of inventory to avoid overstocking, which can restrict airflow and efficiency.
- Energy Efficiency Measures: Regularly audit energy use and invest in features that enhance energy efficiency where possible.
Avoiding Common Mistakes That Lead to Repairs
Being aware of common operational mistakes can prevent many repair scenarios. Mistakes to avoid include:
- Ignoring sounds that deviate from normal operation.
- Overloading the freezer, which can lead to inefficiencies.
- Failing to document temperature fluctuations or irregularities.
- Neglecting to schedule regular professional maintenance checks.
Emergency Walk In Freezer Repair: What to Do
In the event of a breakdown, immediate action can prevent extensive food loss and further damage. Here are crucial steps to follow and considerations when handling emergency repair situations.
Steps to Take When Your Freezer Breaks Down
When your walk-in freezer fails, consider these immediate actions:
- Check electrical connections and ensure the unit is powered.
- Inspect the thermostat settings to confirm they are appropriate.
- Look for visible signs of ice buildup or leaks.
- Maintain appropriate temperature by minimizing door openings and transferring at-risk items to another cold storage if possible.
Contacting Emergency Repair Services
Choosing the right emergency repair service is vital. Key points to keep in mind include:
- Ensure the service is reliable, with technicians who are licensed and experienced in handling commercial refrigeration systems.
- Request a detailed estimate, outlining parts and labor costs.
- Discuss availability for both day and night repairs to handle emergencies at any time.
Preparing Your Freezer for Professional Repair
To facilitate effective repairs, take the following preparatory steps before the technician arrives:
- Clear the area around the freezer to give access to technicians.
- Document any previous repairs or irregularities to inform the technician.
- Ensure safety protocols are followed; disconnect power if necessary.
Post-Repair: Ensuring Continued Efficiency
Once repairs are completed, it’s essential to ensure that the unit continues to function efficiently. Following up a repair can help maintain a stable operation for your freezer.
Testing the Unit After Repair
After repairs, test the unit to ensure functionality:
- Monitor the temperature for a period to confirm it stabilizes within the set range.
- Check the sounds made by the unit to confirm normal operational noise levels.
- Be observant for any leaks or changes in performance post-repair.
Monitoring Temperature and Performance
Continue to monitor the performance closely:
- Keep records of temperature logs to establish trends.
- Review utility bills for unexpected increases indicating potential issues.
Implementing a Regular Maintenance Schedule
Finally, establish a solid maintenance schedule to prevent future issues:
- Set reminders for monthly cleanings and check-ups.
- Evaluate seasonal demands and adjust maintenance accordingly.
- Prioritize hiring professionals annually to inspect and service your equipment.
With the right understanding, you can ensure that your walk-in freezer operates smoothly, remains efficient, and lasts for years to come. Whether you choose to manage some repairs yourself or engage professionals, being proactive is essential to your business’s success.
Leave a Reply