Enhancing Durability and Aesthetics: A Comprehensive Guide to Powder Coating
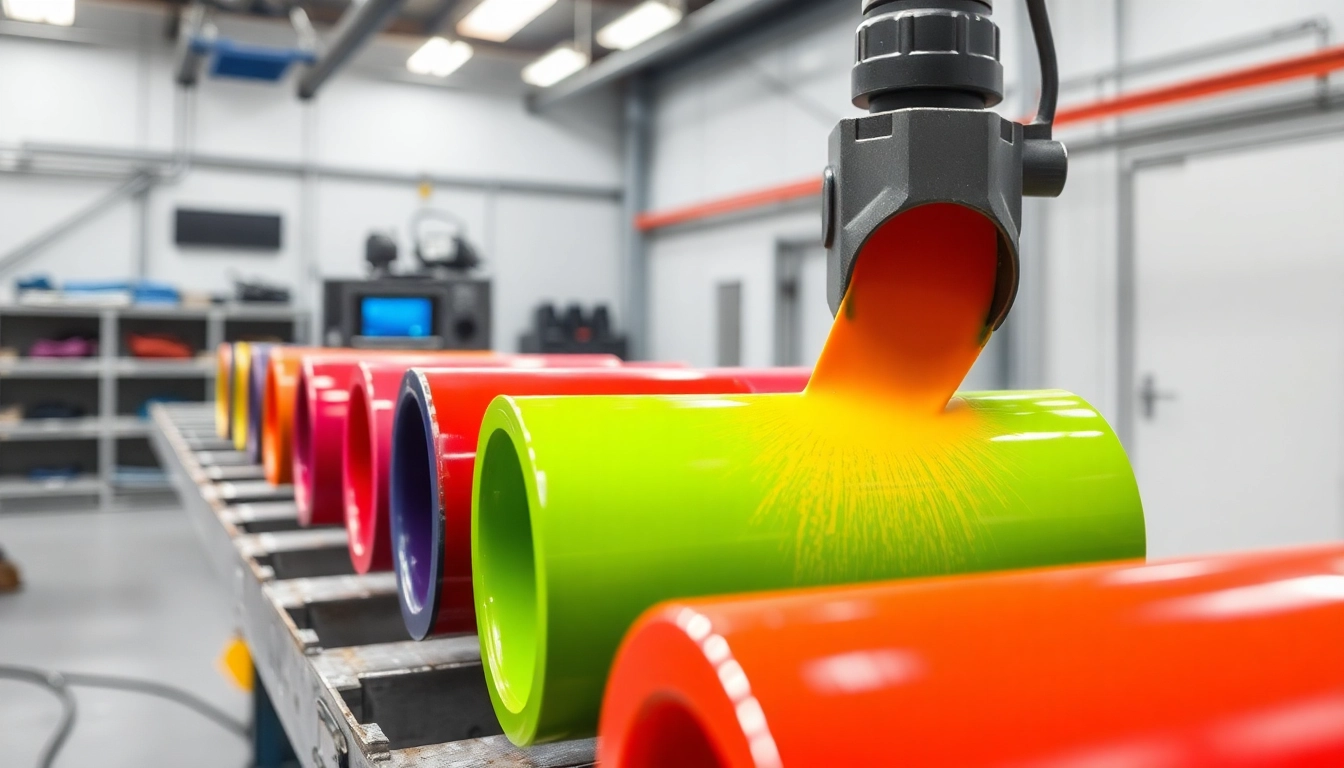
Understanding Powder Coating
What is Powder Coating?
Powder coating is a high-durability finish applied to various surfaces, particularly metals. Unlike traditional liquid paint that relies on solvents, powder coating consists of a free-flowing, dry powder that adheres electrostatically to the surface. This method creates a smooth, uniform finish once baked in a curing oven. The end result is a coating that not only looks great but also enhances durability, making it a favored choice in numerous industries.
The process starts with preparing the metal substrate, followed by the unique application of the powder. Once applied, the item is heated in an oven, allowing the powder to melt and flow together, forming an effective and long-lasting layer. For those interested in exploring this vibrant finishing option, powder coating can provide exceptional results that elevate both appearance and performance.
Benefits of Powder Coating
Powder coating boasts several advantages over traditional painting techniques, making it a preferred choice for manufacturers and consumers alike. Here are some key benefits:
- Durability: Powder-coated surfaces are more resistant to scratches, chips, and fading. This durability is particularly beneficial for outdoor applications exposed to harsh weather conditions.
- Environmental Impact: The powder coating process produces minimal volatile organic compounds (VOCs), making it an eco-friendlier option compared to solvent-based paints.
- Variety of Finishes: Powder coating comes in an extensive range of colors and textures, including glossy, matte, and metallic finishes, allowing for immense customization.
- Cost-Effectiveness: Once the initial setup is complete, powder coating can be more cost-effective in mass production scenarios due to faster application and curing times.
- Safety: The absence of solvents makes powder coating less flammable and safer to handle, not to mention healthier for workers in an industrial setting.
Common Applications of Powder Coating
Powder coating finds its place in many industrial and commercial applications. Some of the most common uses include:
- Automotive Parts: From wheels to body panels, powder coating provides a visually appealing and durable finish.
- Appliances: Household items such as refrigerators and stoves often use powder coating for its heat resistance and long-lasting color.
- Furnishings: Furniture, both indoor and outdoor, is frequently powder coated to enhance aesthetics and resistance to the elements.
- Architectural Components: Railings, window frames, and building facades benefit from the corrosion resistance of powder coatings.
- Electrical Enclosures: Equipment housings and fixtures are powder-coated to prevent environmental damage and improve visual appeal.
The Powder Coating Process
Preparation and Pre-Treatment Steps
The powder coating process begins long before the application of the powder itself. Thorough surface preparation is crucial for achieving optimal adhesion and durability. This preparation usually involves several critical steps:
- Cleaning: The metal surface must be free of dirt, grease, and debris. Common methods include solvents, detergents, and acid solutions.
- Degreasing: Specialized cleaning agents break down oily residues or contaminants that can hinder adhesion.
- Surface Etching: The use of chemical etchants or abrasive blasting roughens the surface, increasing its ability to bond with the powder. This step is vital for enhancing the mechanical grip of the coating.
- Rinsing and Drying: After cleaning and etching, rinsing ensures that no residues remain. Surfaces must then be dried to prevent moisture-induced defects during application.
Application Techniques for Powder Coating
After surface preparation, the powder coating is applied using specific techniques that ensure even coverage and optimal results. The most popular application methods include:
- Electrostatic Spray: This is the most common application method, where charged particles of powder are sprayed onto the grounded surface. The electrostatic charge ensures uniform coverage.
- Fluidized Bed Coating: The part is heated and dipped into fluidized powder, which adheres to the surface. This method is best for large items or those with complex shapes.
- Pneumatic Application: Powder is fed into a spray gun that uses compressed air to atomize the powder and apply it to the substrate.
Curing and Finishing Processes
Once the powder is applied, the next step involves curing. This is a crucial part of the process that transforms the powder into a durable finish:
- Curing Oven: Parts are placed in a curing oven typically set between 350°F to 400°F (about 177°C to 204°C) for a specified amount of time, depending on the product’s specifications.
- Cooling: After curing, parts are gradually cooled to room temperature. This cooling period is essential for stabilizing the coating and ensuring long-lasting performance.
- Quality Control: Final inspections are conducted to ensure uniformity, thickness, and adherence of the coating. Any defects can lead to rework or rejection of the coated components.
Choosing the Right Powder Coating
Types of Powder Coatings Available
With various powder coatings, selecting the right one depends on the application and specific requirements:
- Thermosetting Powder Coats: These powders undergo a chemical change when heated, resulting in a hard, durable finish that is heat and chemical resistant.
- Thermoplastic Powder Coats: These do not undergo a chemical change and can be remelted. They are more flexible and may be better suited for items that face repeating stress.
Factors Affecting Selection
When deciding on a powder coating, consider the following factors:
- Environmental Exposure: Assess the environment (e.g., outdoor exposure, moisture, chemicals) to select a coating that meets durability requirements.
- Finish Requirements: Choose a coating that meets aesthetic criteria, from colors to textures.
- Regulatory Compliance: Especially for industrial applications, ensure that the coating meets applicable safety and environmental regulations.
Color Trends in Powder Coating
As trends evolve, color choices in powder coating have expanded dramatically. The latest trends lean towards:
- Bold Colors: Vibrant, eye-catching colors are increasingly popular, especially in consumer goods and automotive finishes.
- Textured Finishes: Textures such as matte or satin not only offer aesthetic appeal but also enhance grip and reduce scratches.
- Custom Colors: Tailored options, reflected in custom formulations or colors matching specific brands or products, continue to rise in demand.
Cost Considerations and Value of Powder Coating
Estimating Powder Coating Costs
The cost of powder coating can vary widely based on several factors:
- Item Size: Larger parts typically increase the cost due to larger amounts of powder and extended curing times.
- Material Preparation: Additional pre-treatment requirements may impact overall cost.
- Color and Finish: Custom colors or specialized finishes can also add to the expense.
Cost Comparison: Powder Coating vs. Painting
While both powder coating and liquid paint serve similar purposes, their costs can differ:
- Initial Investment: Powder coating often requires a higher initial setup cost, primarily due to equipment and facility modifications.
- Long-Term Value: However, given the durability and reduced frequency of touch-ups or refinishing, powder-coated items may prove more economical in the long run.
Return on Investment Through Powder Coating
Understanding the ROI of powder coating involves analyzing both direct and indirect benefits:
- Increased Durability: The long lifespan of powder-coated surfaces can translate to fewer replacements and repairs.
- Enhanced Product Appeal: Visually appealing finishes can lead to higher sales prices or enhanced consumer preference.
- Efficiency Gains: The faster curing and application processes translate to increased production output for businesses.
Future of Powder Coating Technology
Innovations in Powder Coating
As technology advances, powder coating continues to evolve. Innovations include:
- Advanced Formulations: New powder formulations with properties like UV resistance and additional color stability are becoming available.
- Smart Production Techniques: Automation and improved process controls increase precision, reducing waste and improving efficiency.
- 3D Printing Integration: New applications utilize 3D printing technology to produce customized parts that can be easily coated.
Sustainability Practices in Powder Coating
In an era focused on sustainability, the powder coating industry is responding with various eco-friendly practices:
- Recycling of Powder: Unused powders can often be reused, minimizing waste and costs.
- Eco-Friendly Formulations: Development of powders that are free of hazardous materials and comply with environmental regulations.
- Energy Efficiency: Enhanced oven designs that consume less energy during the curing process.
The Rise of Eco-Friendly Powder Coating Options
In line with sustainability trends, environmentally friendly powder coatings are gaining traction. These options include:
- Water-Based Powders: Alternatives that use water as a solvent, leading to reduced VOC emissions.
- Biodegradable Powders: Innovations in the development of biodegradable materials for environmentally conscious applications.
Leave a Reply