Elevate Your Home with Coastal Metal Roofing: Durability Meets Design
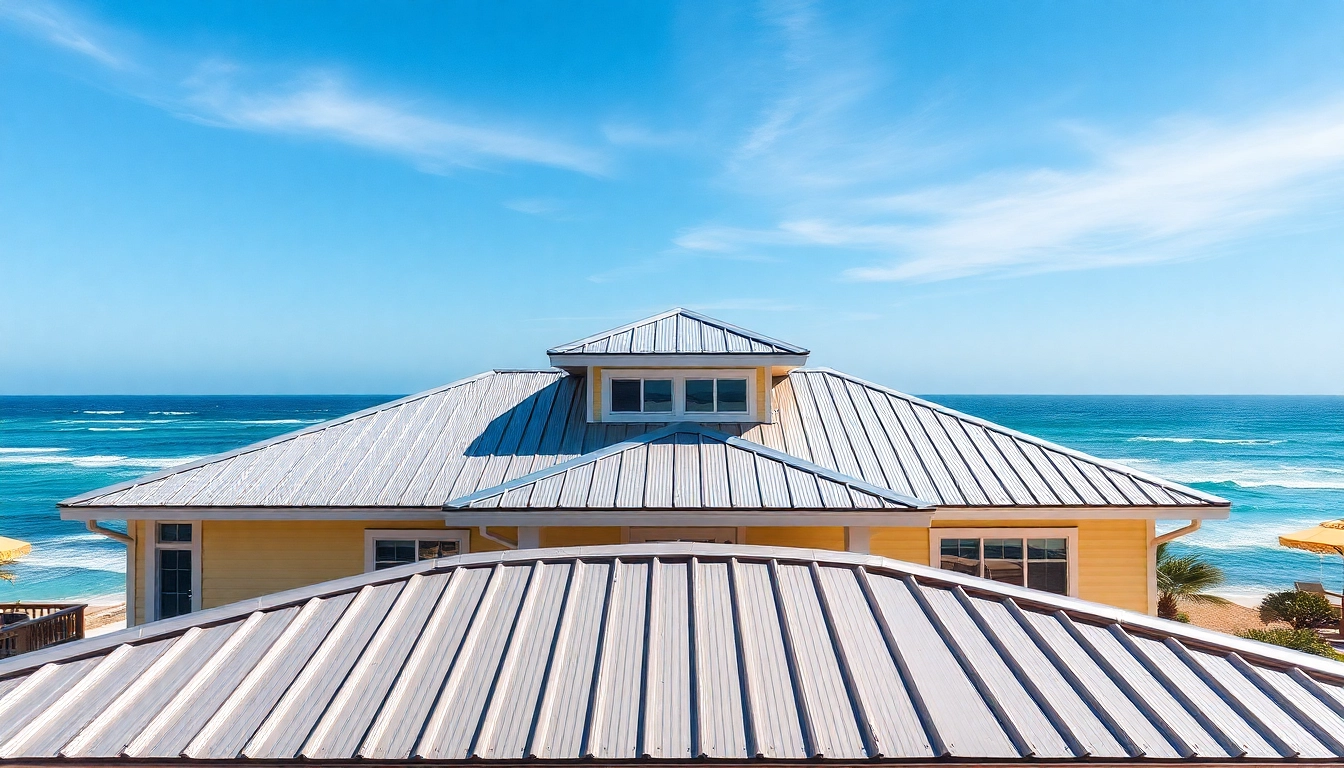
Introduction to Coastal Metal Roofing
As the demand for durable and resilient building materials continues to rise, coastal metal roofing emerges as a leading choice for homeowners and builders in coastal areas. Given the unique environmental challenges faced in such regions, including high winds, salt spray, and humidity, selecting the right roofing material is crucial for the longevity and performance of structures. This article explores the ins and outs of coastal metal roofing, including its types, benefits, installation process, maintenance practices, and case studies that showcase its effectiveness.
What is Coastal Metal Roofing?
Coastal metal roofing consists of roofing systems specifically designed to meet the demands of coastal environments. These roofing materials are typically made from metals such as steel, aluminum, or copper, which are treated or coated to enhance their resistance to corrosion, fading, and rust. Metal roofing systems are characterized by their interlocking panels, durability, and variety of styles, making them an appealing choice for both residential and commercial buildings near waterfronts.
Benefits of Coastal Metal Roofing
Choosing coastal metal roofing offers numerous advantages, particularly for properties located in marine climates:
- Durability: Designed to withstand harsh weather conditions, metal roofs can resist wind speeds of up to 140 mph, standing strong against coastal storms and hurricanes.
- Corrosion Resistance: Coastal metal roofing materials are often coated with special finishes that protect against salt spray and moisture, significantly extending their lifespan.
- Energy Efficiency: Reflective coatings can reduce heat absorption, leading to lower cooling costs and making metal roofing a more energy-efficient choice.
- Environmentally Friendly: Many metal roofing materials are made from recycled content and are fully recyclable at the end of their lifespan, appealing to eco-conscious homeowners.
- Aesthetic Variety: Available in various styles and colors, coastal metal roofing can replicate traditional roofing materials, offering aesthetic flexibility without compromising performance.
Choosing the Right Metal for Coastal Environments
The choice of metal is crucial for the performance of coastal metal roofing. Here are some common options:
- Aluminum: Lightweight and highly resistant to corrosion, aluminum is widely preferred for coastal constructions. Its natural resistance to the elements makes it an excellent choice for seaside homes.
- Galvalume Steel: Combining the strength of steel with a protective coating of aluminum and zinc, Galvalume is known for its outstanding rust resistance and durability.
- Stainless Steel: Though more expensive, stainless steel offers superior corrosion resistance and is ideal for high-end coastal installations.
- Copper: Renowned for its longevity and natural beauty, copper roofs develop a patina that protects against corrosion, making them an elegant choice for upscale coastal properties.
Installation Process for Coastal Metal Roofing
Preparation and Planning Steps
Effective installation of coastal metal roofing requires careful planning and preparation to ensure that roofs can withstand the elements over the long term. Here are key steps:
- Site Inspection: Before installation, conduct a thorough inspection of the site to assess exposure to wind, rain, and salt. This assessment will help in determining the specific type of metal and installation technique required.
- Choosing Panels: Select the right type of metal roofing panels based on the design of the building and local climate conditions. Utilizing panels with adequate wind resistance is crucial.
- Gathering Permits: Ensure that all necessary building permits and compliance with local codes are obtained before proceeding.
Essential Tools for Installation
Having the right tools is imperative for a successful installation. Essential tools include:
- Metal shears or snips for cutting panels
- Drills and fasteners specifically designed for metal roofing
- Chalk lines for accurate panel placement
- Ladders and safety equipment for working at height
- Sealing tape and caulking guns for weatherproofing joints
Step-by-Step Installation Guide
- Setting the Framework: Install the necessary underlayment and framework to support the roofing panels, ensuring proper slope for water drainage.
- Aligning Panels: Start at the bottom edge and work your way up, aligning panels precisely as per manufacturer guidelines.
- Securing Panels: Use the appropriate fasteners and techniques to secure the panels, taking care to avoid over-tightening which may warp the material.
- Sealing Joints: Apply sealant to prevent water infiltration at overlaps and joints, enhancing the roof’s waterproof properties.
- Final Inspection: Conduct a comprehensive inspection post-installation to ensure everything is properly secured and sealed, checking for any exposed fasteners or gaps.
Best Practices for Maintenance and Longevity
Regular Maintenance Tips
The longevity of coastal metal roofing greatly depends on regular maintenance practices. Here are some tips to ensure optimal performance:
- Clean debris regularly to prevent mildew and rust, especially in coastal areas where organic buildup can accelerate decay.
- Inspect for loose or damaged panels after severe weather events, ensuring all fasteners are secure.
- Apply a rust-inhibiting paint or coating periodically, depending on the material used for additional protection.
Common Issues and Solutions
Even the best roofing can encounter challenges. Here’s how to tackle common issues:
- Creaking or Noisy Roof: If the roofing panels are too tightly fastened, they may creak when expanding and contracting. Adjusting fastener tightness can resolve this.
- Corrosion: While many metal roofs come with protective coatings, corrosion can still occur. Affected areas can be treated with rust-inhibiting spray.
- Leaking: Inspect sealant and fastener integrity if leaks develop, resealing or replacing components as necessary to restore waterproof performance.
Seasonal Checks and Upkeep
Seasonal inspections are vital for maintaining coastal metal roofs:
- Spring: After winter storms, check for loose panels and signs of corrosion.
- Summer: Inspect for debris accumulation from trees or summer storms.
- Fall: Prepare for winter by confirming that all seals are intact and that the roof is clean.
Cost Considerations for Coastal Metal Roofing
Estimating Material Costs
The cost of coastal metal roofing can vary depending on factors such as the type of metal selected, roofing style, and local market conditions. On average, homeowners can expect to pay between $5 and $12 per square foot for materials alone. However, these costs can fluctuate based on the following:
- Type of metal
- Design complexity
- Geographical area
Labor Costs and Budgeting
Labor costs will also significantly impact the total investment for coastal metal roofing. Factors to consider include:
- Experience and expertise of installers
- Local labor rates
- Complexity of the installation process
On average, labor can account for 20-40% of the total project cost, making it essential to budget carefully and choose qualified contractors.
Long-Term Savings and ROI
While coastal metal roofing may have a higher upfront cost compared to traditional roofing materials, its long-term benefits offer significant return on investment. Key savings include:
- Lower energy bills due to thermal efficiency
- Reduced maintenance costs over the roof’s lifespan
- Potential for lower homeowner’s insurance premiums due to enhanced durability against severe weather events
Case Studies: Successful Coastal Metal Roofing Projects
Residential Success Stories
Multiple homeowners have transitioned to coastal metal roofing with remarkable results. A prime example includes a beachfront property that installed aluminum roofing, leading to:
- Decreased energy consumption by 30% year-round due to reflective coatings.
- Enhanced property value upon resale, attributed to the roof’s durability and aesthetic appeal.
Commercial Applications
Commercial buildings, particularly in tourist-heavy coastal towns, have also benefited from metal roofing systems. A retail complex in Florida reported:
- 47% less maintenance costs compared to a traditional shingle roof, with fewer repairs needed over time.
- A substantial increase in foot traffic attributed to the building’s attractive exterior.
Impact on Property Value
Investing in coastal metal roofing can significantly enhance property values. Market data suggests properties featuring high-quality metal roofs often command a premium of 30% over comparable homes without this feature, largely due to increased perceived durability and style.
Leave a Reply